Participation Chartwell Consulting Debottlenecking Workshop in Karlsruhe
Chartwell Consulting Debottlenecking Workshop
On January 23, 2020, we attended the Chartwell Consulting Debottlenecking Workshop in Karlsruhe, Germany.
The two-hour interactive workshop involved developing strategies for increasing production in a multi-stage production process, discussing them in groups, and finally evaluating their efficiency and feasibility. At the beginning, Michaela Gratzfeld and Gustav Keppler introduced the Karlsruhe ISPE Student Chapter to the participants. Chartwell Consulting was then presented to us by the Chartwell staff.
Chartwell Consulting is a management consulting firm that helps other companies uncover hidden potential in their operations and quickly turn it into operational and financially measurable improvements. For this purpose, a carefully selected team takes care of the customer, and the consultation is divided into several sub-operations:
Assessment (1-2 weeks): The scope of opportunities in the company is assessed by working closely with company staff to understand existing barriers and performance limitations.
Pilot (1-2 months): There will be an exchange with representatives from all departments of the company to demonstrate how much potential there is during a pilot project.
Project (2-6 months): With result-oriented methodology, the team tries to achieve more results and profit. In the process, the rest of the company is led by the team in the change process.
After the consultant leaves: Efforts are made for ongoing change and sustainable impact to maintain the status quo of increased productivity.
Chartwell Consulting has been around for about six years and operates worldwide. The approximately 50 employees are distributed among the locations Berlin (Germany), London (England) and Boston (USA).
For the workshop, Chartwell staff devised a program that involved using a case study to find potential bottlenecks, evaluate any performance improvement strategies, and put them to good use. The case study involved a chemical process followed by preparation of the resulting product. Based on various parameters (e.g. process speed, process utilization, …), the task was to work out the speed-limiting step (“bottleneck”) in groups of three. Afterwards, Chartwell staff presented the solutions that are provided, for example, by the company being consulted. The aim here was to evaluate the effectiveness of the solution approaches. The difficulty was that only limited information was available on cause and effect. E.g. to increase the efficiency of the reactor heating, the cooling coil of the heat exchanger can be cleaned with the aim to improve the heat transfer coefficient to heat up the reactor faster.
However, there are no measurement results of the heat transfer coefficient and both the time of the employees and the appropriate technical requirements for measurement are not available. Thus, with the help of further considerations, it had to be worked out whether other parameters do not also have a positive effect on the increase in production, such as the temperature, which can be measured at the inputs and outputs with temperature sensors.
As a result, it was possible to estimate from temperature profiles in the reactor and cooling coils that cleaning would not have the desired effect of increasing process performance. But might a greater flow rate in the cooling coils help using a new valve or a different flow medium? These and other strategies for improving productivity were highlighted and evaluated in detail. It was also necessary to estimate which optimization is best when all methods serve to increase performance.
In addition to the scientific aspects, the participants were also impressively made aware of the company-political and social realities. Because not every responsible employee is always available or has time to take care of problems during strategy development (such as querying characteristic data, fetching new improved machine parts from the warehouse, …). In addition, it is necessary to take into account a decent communication and adequate interaction with the customers, on the one hand, the necessary simplification of the problem and, on the other hand, the target-specific question to deal with the development of the method. This was highlighted by the high-quality acting skills of Chartwell employees (e.g., how do you deal with a bad-tempered Head of Engineer who doesn’t always volunteer advice and assistance). In the meantime, tips for dealing with customers or problems were discussed again and again. Furthermore, the group dynamics of the workshop participants were promoted, as any problems were solved and solutions were worked out together.
After a final discussion on the part of Chartwell and the thoroughly positive feedback from the participants, the debottlenecking workshop was over after a good two hours. A big thank you goes out to the Chartwell Consulting staff for the carefully crafted program and dedication in running the workshop and to Michaela Gratzfeld and Gustav Keppler for organizing the event. We look forward to more exciting collaborations with Chartwell.Your Maximilian Ell
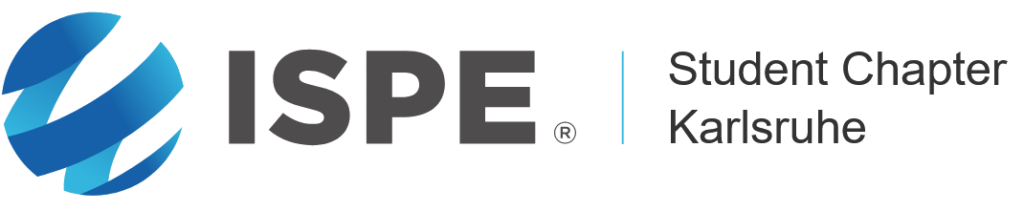